Starting a commercial-scale brewery requires some serious, specialized gear that can handle large batches and includes automation. Whether you’re kicking off a new craft brewery or upgrading your current setup, investing in top-notch brewing systems is key for efficiency, safety, profitability, and consistent flavor. This guide covers the must-have brewery equipment.
Key Brewery Equipment
The beer production process involves several critical steps, each requiring specific equipment:
- Milling: Roller mill, hammer mill
- Mashing: Mash tun
- Lautering: Lautering tun, rakes, sparging system
- Boiling: Brew kettle, wort chiller
- Fermenting: Fermentation tanks, temperature control
- Maturation: Serving tanks, filters
- Packaging: Bottler, canner, keg washer, labeler
- Cleaning: CIP systems, detergent pumps, hoses, spray balls
Selecting Brewing System Suppliers
When sourcing brewery equipment, consider the following factors for selecting suppliers:
- Experience: Years of expertise in building systems for commercial breweries of similar capacity
- Customization: Ability to tailor the system to your space, pack sizes, and brewing process
- Quality: Use of stainless steel and sanitary elements
- Automation: Level of automatic operation, detectors, and manual oversight required
- Service: Installation service, operator training, maintenance, and repair services
- References: Client references to gauge quality and reliability
Reputable manufacturers offering comprehensive brewing systems include Rolec and Brewmation. Prices for a 15-barrel brewhouse range from $100,000 to $500,000. It is advisable to obtain multiple quotations before making a decision.
Tips for Choosing the Best Brewery Equipment
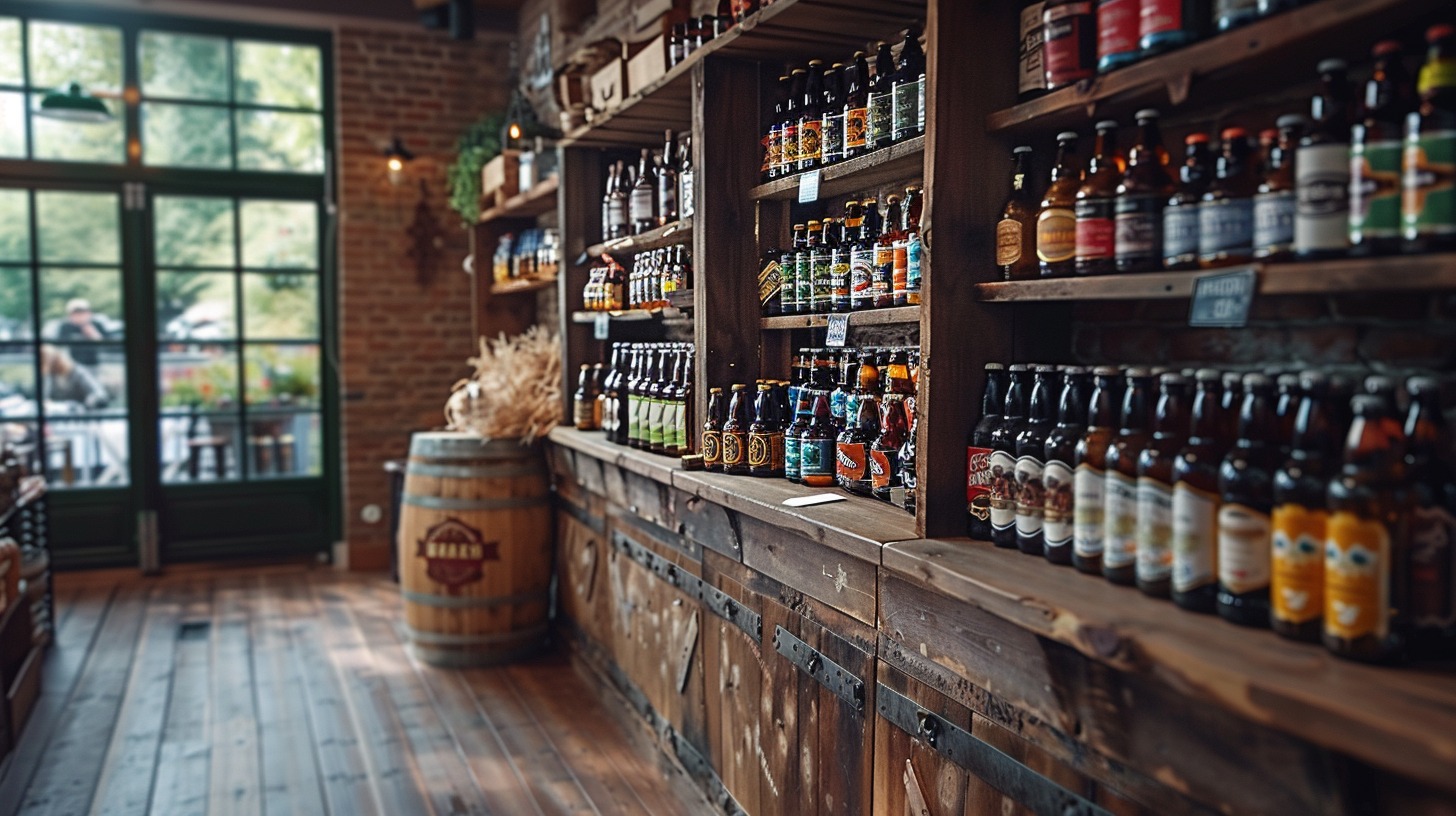
When evaluating and funding brewing equipment, consider the following tips to ensure quality and efficiency:
- Production Scale: Align equipment batch sizes and vessel capacities with your current production needs and projected volumes for the next five years.
- Quality and Durability: Opt for stainless steel components designed to meet strict hygiene and safety criteria.
- Space Considerations: Accurately measure your available floor space and layout to ensure ample room for tanks and other equipment.
- Automation for Consistency: Choose automated systems to achieve precise temperature control and minimize contamination risks.
- Clean-in-Place (CIP): Select equipment with CIP capabilities, including spray balls, hoses, and pumps, for efficient cleaning.
- Flexibility for Innovation: Invest in modular systems that can adapt to process changes and accommodate special brews.
- After-Sales Service: Ensure the vendor provides comprehensive support, including operator training, maintenance, and spare parts.
Investing in top-quality stainless steel brewing equipment that meets the criteria for automation, customization, and durability will pay off in long-term, consistent craft beer production.
Tips for Operating and Maintaining Brewery Equipment
To keep your brewing system reliable over the long haul, stick to these key tips: create detailed SOPs and train your team well, keep an eye on performance metrics, do regular visual checks, clean thoroughly after each use, lubricate and calibrate moving parts, check safety mechanisms, schedule preventative maintenance, and maintain a stock of essential spare parts. Following these steps will keep your brewhouse running smoothly.
How Long Does It Take to Build and Install a Brewery?
Building a brewery usually takes anywhere from 6 months to 2 years, depending on the project’s size. Key phases include planning and design, procurement and manufacturing, setup and installation, and staff training and launch. Start planning 1-2 years ahead to fit in construction, equipment fabrication, and testing.